ASSIGNMENT #9
IE 323 – Fall 2019
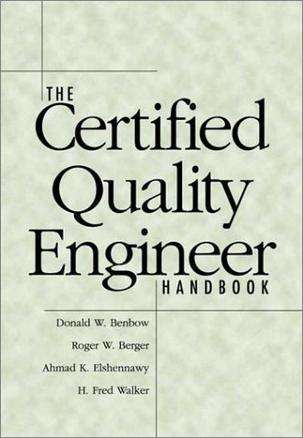
quality engineer代写 A quality engineer applied control chart methodologyto the manufacturing of a horseshoe-shaped metal fastener called a robotics clamp.
Due Date: Friday, 12/13, by noon Textbook: p. 706-707 2, 3, 4, 8, 9, 10
Note: This assignment is optional. If you turn it in, your homework average will be calculated based on 9 total assignments, dropping the lowest grade of the 9, and averaging the remaining 8 assignments. If you do not turn it in, your homework average will be calculated based on 8 total assignments, dropping the lowest grade of the 8, and averaging the remaining 7 assignments. The solution for this assignment will be posted on CANVAS sometime after noon on Friday, 12/13.
1.A quality engineer applied control chart methodology to the manufacturing of a horseshoe-shaped metal fastener called a robotics clamp. quality engineer代写
Users of the clamp were concerned with the width of the gap between the two ends of the fastener. Their preferred target width is 0.054 inches. An optical measuring device was used to measure the gap width of the fastener during the manufacturing process. The manufacturer sampled five finished clamps every 15 minutes throughout its 16-hour daily production schedule and optically measured the gap. Data for 4 consecutive hours of production are presented in the following table.
Gap Width quality engineer代写
Time (thousandths of an inch) _____
00:15 54.2 54.1 53.9 54.0 53.8
00:30 53.9 53.7 54.1 54.4 55.1
00:45 54.0 55.2 53.1 55.9 54.5
01:00 52.1 53.4 52.9 53.0 52.7
01:15 53.0 51.9 52.6 53.4 51.7
01:30 54.2 55.0 54.0 53.8 53.6
01:45 55.2 56.6 53.1 52.9 54.0
02:00 53.3 57.2 54.5 51.6 54.3
02:15 54.9 56.3 55.2 56.1 54.0
02:30 55.7 53.1 52.9 56.3 55.4
02:45 55.2 51.0 56.3 55.6 54.2
03:00 54.2 54.2 55.8 53.8 52.1
03:15 55.7 57.5 55.4 54.0 53.1
03:30 53.7 56.9 54.0 55.1 54.2
03:45 54.1 53.9 54.0 54.6 54.8
04:00 53.5 56.1 55.1 55.0 54.0
(a)The quality engineer is trying to establish the control limits for an and R chart. Using the data, compute the centerline and control limits for an R chart. Plot the points. Is the process in statistical control?
(b)Compute the centerline and limits and draw the chart. Does the process mean appear to be in control? quality engineer代写
(c)Assume that the assignable cause for the out-of-control point(s) is found and corrected. Eliminate the out-of-control point, recompute the limits and redraw both the R chart and the chart. Does the process appear to be in control now?
(d)Once the process is in control, estimate the mean and standard deviation for the process.
(e)Specifications require the gap width of a clamp to fall within 54 ± 4 thousandths of an inch. Estimate the fraction nonconforming number of clamps.
(f)Estimate the Cp and Cpk. Comment on their results.
2.To monitor the manufacturing process of rubber support bearings, quality engineer代写
a quality engineer randomly selects 100 bearings from the production line, each day over a 15-day period. The bearings were inspected for defects and the number of defectives found each day is recorded.
Day | Number of Defectives |
1 | 2 |
2 | 12 |
3 | 3 |
4 | 4 |
5 | 4 |
6 | 1 |
7 | 3 |
8 | 5 |
9 | 3 |
10 | 2 |
11 | 10 |
12 | 3 |
13 | 3 |
14 | 2 |
15 | 3 |
(a)Construct a fraction nonconforming control chart for the bearings.
(b)Does the process appear to be in control? If not, outline what steps should be taken next (do not carry them out).
3.High level computer technology has developed bit-sized microprocessors for use in operating industrial robots. To monitor the defective microprocessors produced by a manufacturing process, 50 microprocessors are sampled each hour. The results for 20 hours of sampling are provided below.
SampleDefectives | 15 | 26 | 34 | 47 | 51 | 63 | 76 | 85 | 94 | 105 |
SampleDefectives | 118 | 123 | 132 | 141 | 150 | 161 | 171 | 182 | 193 | 203 |
Construct a control chart for the number of defective microprocessors. Does the process appear to be in control?
4.The following data represent the number of nonconformities on 22 samples (production days in July) of 50 EGA cards.
SampleNumber | Number of Nonconformities | Sample Number | Number of Nonconformities |
1 | 12 | 12 | 28 |
2 | 6 | 13 | 14 |
3 | 14 | 14 | 15 |
4 | 11 | 15 | 13 |
5 | 16 | 16 | 2 |
6 | 9 | 17 | 9 |
7 | 11 | 18 | 10 |
8 | 17 | 19 | 14 |
9 | 8 | 20 | 11 |
10 | 13 | 21 | 13 |
11 | 21 | 22 | 16 |
(a)Develop an appropriate control chart to determine if the process is in statistical control.
(b)Compute the centerline and control limits for the control chart for the average number of nonconformities per unit. Do not redraw the chart.
5.In a study conducted to estimate gage repeatability and operator reproducibility,
two operators use the same gage to measure 5 parts each, repeating the measurements three times for each part. The data are shown below. (Please carry out your calculations to two significant digits after the decimal point). quality engineer代写
Part Number | Operator 1 Measurements | Operator 2 Measurements | ||||
1 | 2 | 3 | 1 | 2 | 3 | |
12345 | 54545 | 44545 | 54455 | 54435 | 54445 | 45446 |
(a)Estimate gage repeatability and reproducibility.
(b)Estimate the standard deviation of measurement error.
(c)If the specifications are at 50 ± 10, what can you say about gage capability?
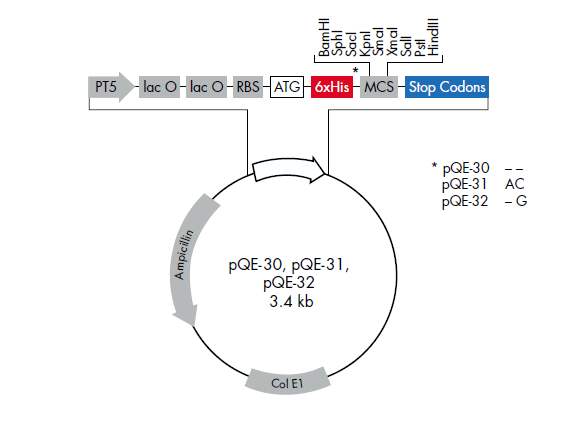
您必须登录才能发表评论。